Description
Machine Operation
A simple Chain Drive connects the PowerPinner 50 and the coil line’s insulator. This drive powers the heads forward at the same speed as the sheet metal whenever the machine is pinning. Immediately after the machine stops pinning, air cylinders move the drive heads back towards the insulator. The PLC optimizes the head travel so that full ten-foot sheets may be insulated with pins on six inch centers. The split pin track keeps a reserve of pins ready to speed load in the lower track every time the heads return to the home position.
Additional Features
Programmable Logic Controller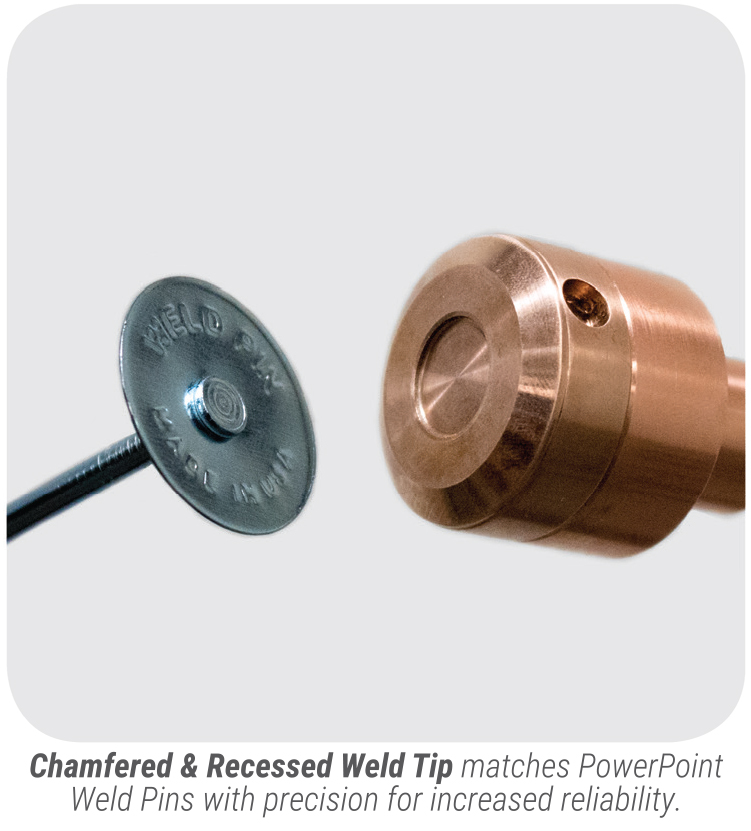
Inside the control box is a PLC, which has been programmed here in the USA, to coordinate welding and machine function resulting in the fastest and most perfected weld every time. Machine operators only need to increase the weld setting for longer pins or thicker sheet metal, and the PLC will set the dwell time and coordinate the feed cycle. Minimal operator training is needed for this machine which means maximum flexibility. The PLC even has a diagnostic screen should a machine element require attention. The PLC allows for minimum operator intervention during setup or job changes, all while producing maximum performance at industry leading speeds.
Chamfered & Recessed Weld Tip
The magnetic upper weld tip is specifically designed with a chamfered edge and recessed center to optimize the weld quality of PowerPoint weld pins. The unique characteristics of the PowerPoint weld pin’s noninvasive protruding shank captures and centers the weld pin to ensure consistent loading, while the beveled retaining cap prevents it from shifting off the weld tip when the pin is being set through the insulation. Although the PowerPinner 50 works with a variety of weld pins, using our PowerPoint’s precision manufacturing process assures a trouble free operation with the best quality weld possible.
Double-Acting Load Cylinder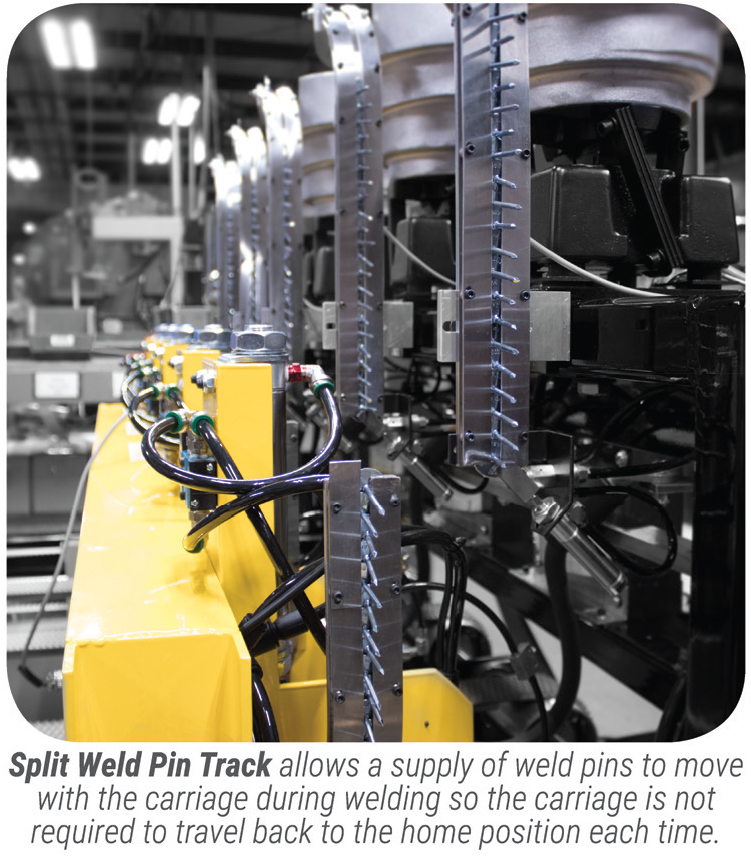
To keep up with the intense speeds of the PLC, double-acting load cylinders are standard on every machine. This ensures that each Weld Pin is loaded at maximum speeds without the danger of a component collision potentially possible with single-acting cylinders, which may lag due to its dependence on spring tension.
Simplified Controls
A single weld-setting switch controls the weld time while the PLC optimizes the dwell time. The other controls are individual Weld Head on/off switches and matching feeder bowl speed control.
Safety – A high visibility power switch comes standard with a simple to use Lockout/Tagout feature.
NEMA® Type 12 Electrical Enclosures
To prevent vital components from the rigor of most manufacturing environments, every electrical enclosure is rated to the National Electrical Manufacturers Association’s Type 12 standards. This protects your investment from dust, debris, adhesive remnants and oil vapor from reaching operating critical components.
Moving Carriage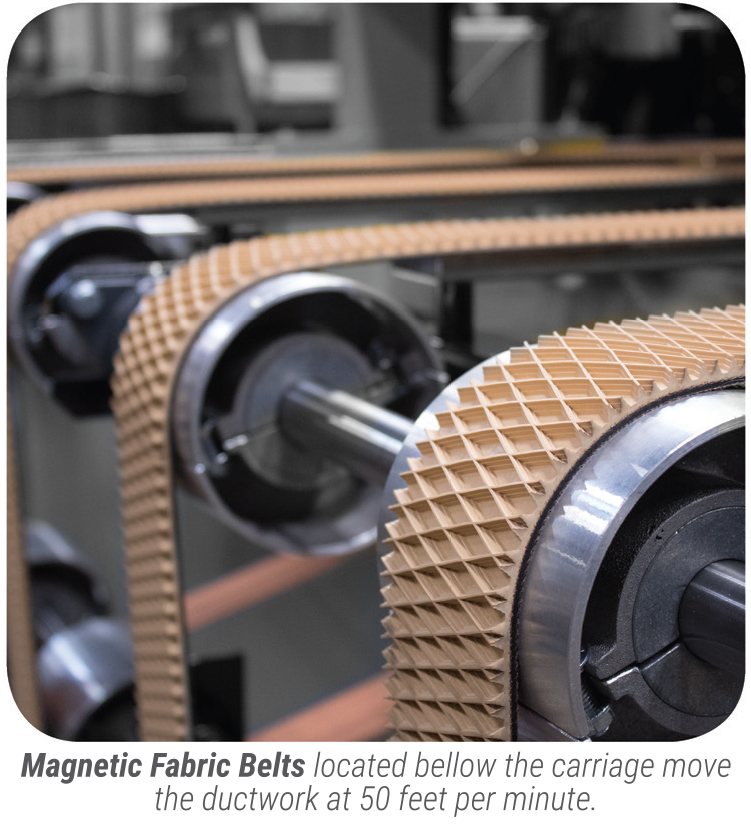
The lightweight aluminum carriage allows the PP50 to operate at the same 50 feet per minute pace that the fiber belts move the duct work.
Magnetic Drive Belts
The magnetic drive belts hold the sheet metal in place and keep insulation ductwork from shifting. This allows for precision and uniform welds in large ductwork. Two electronic clutches at the end of the drive belts push the carriage to match coil line speeds.
Optional SAM Controller – The Spacing Acquisition Module replaces damaged or outdated control systems on older coil lines.